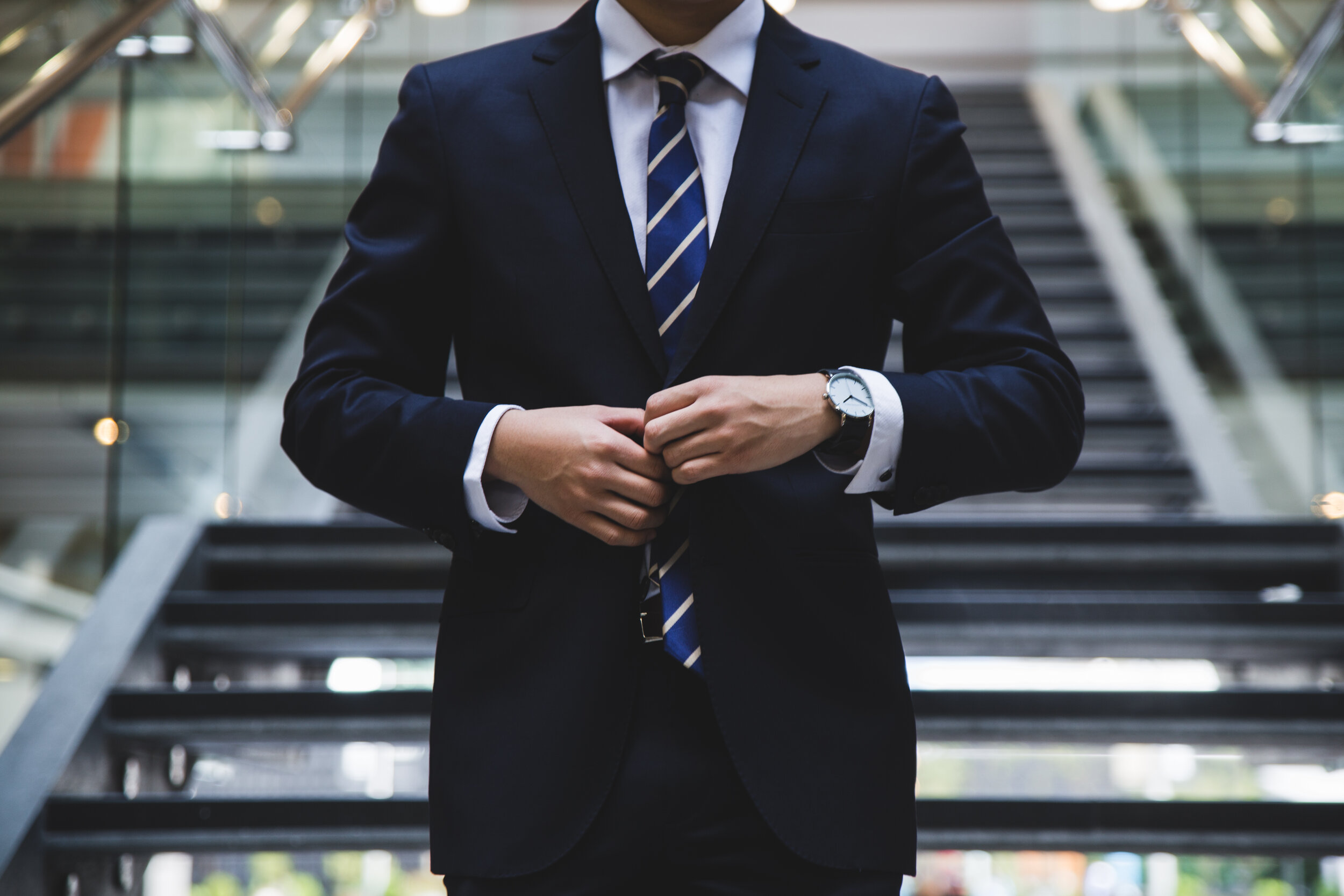
Robust Design
Robust Design
For mechanical product development - Robust Design is the discipline of reducing sensitivity towards part-part variation in production. Having a robust design will generally allow a company to improve cost and performance of products as well as having a more controlled product development process with bigger predictability. Robustness is achieved by looking into disciplines like kinematics, structure calculations, DFM, DFA and tolerances.
KTW and RD8 drives Robust Design through a framework of 8 systematic and objective design disciplines:
A framework piloted by 8 systematic and objective design disciplines
KINEMATICS - ASSESSING PRODUCT ARCHITECTURE & DESIGN QUALITY
FUNCTIONS - PREDICTIVE PERFORMANCE MODELING, SENSITIVITY AND DPMO
COUPLINGS - ADVERSE INTERLINKAGE BETWEEN MODULES, BODIES, PARTS AND FUNCTIONS
TOLERANCES - SPECIFICATION MATCH TO CAPABILITY + QUALITY OF DEFINITION
STRUCTURE - PERFORMANCE LEVEL OF LOAD CASES
MATERIALS - MATERIAL SELECTION FIT FOR PURFOSE AND PAIRING
DFM - MANUFACTURABILITY MATURITY
DFA - ASSEMBLY STATES AND STABILITY, INTERFACES AND ORIENTATION
Advantages of Robust Design
Greener
ENABLEMENT OF GREEN MATERIALS (50~100%)
- Replacement of virgin materials with recycled alternatives or bioplastics
REDUCTION OF MATERIAL CONSUMPTION (5~80%)
- Over-engineering
- Geometry optimization
- Scrap reduction in production and assembly
UPCYCLING & CIRCULAR DESIGN
- Improving ability for service, spare parts and disassembly
DOWNSTREAM ACTIVITIES (5~20%)
- Lower energy consumption of products
- Increase product lifetime
GREEN PART PRODUCTION (5~30%)
- CO2 reductions by production changes or production efficiency gains
SIMPLER
COMPLEXITY REDUCTION
- Reduction of number of tolerances
- Reduction of tolerance levels
- Reduction of functional surface areas
- Reduction of system dependencies
- Simplified assembly
- Optimization and standardization of interfaces & modules
- Commonalization - Standarization across products and platforms
Cost Reduction (5~30%)
- Reduction of scrap & customer complaint rates/recalls
- Enablement of low-cost suppliers
- Enablement of low-cost production processes
- Volume consolidation / modularization
- Reduction of development time
- Reduction of ramp-up time / iterations
- Reduction of time used in assembly(assembly/automation improvements by design)
- Less CAPEX investments - low cost equipment & tools
FASTER
REDUCTION OF DEVELOPMENT TIME (10~50%)
Reduction of development timeline & resources by;
- Systematic work with 8 leading indicators for the robustness of a mechanical design
- Design guides/best practices
- Robust Design Productivity tools/software
- People - talent development
BETTER PRODUCTION PERFORMANCE (5~50%)
- Enablement of faster assembly times
- Enablement of optimized automation levels
REDUCTION OF RAMP-UP TIME(10~50%)
- Reduction of engineering detours
- Reduction of tooling iteration
- Reduction of noise factors(for assembly, equipment and product)
SMARTER
INCREASED PRODUCT PERFORMACE (5~50%)
Examples;
- Increased energy efficiency
- Increased product lifetime
- Increased weight performance
NEW LEAPS OF INNOVATION
- New patents
- Radical optimization of main product functions
- Optimization across product-man-machine
- Data dreiven product development
INCREASED PERCERIVED QUALITY (5~50%)
Examples;
- Reduced backlash
- Improved accuracy
- Improved aesthetics/split lines
- Improved consitency across products
INTRODUCTION OF NEW FEATURES
- Improved success rate of new product platform dev.
- Improved success rate of new technology introduction
- Improced success rate of new features/modules
